Xeikon pursuing pathway to lights out
Digital print solutions pioneer Xeikon says its vision of full digitisation in print manufacturing is becoming a reality, as it launches new areas of innovation in presses, services and workflow, which it says will lead to lights out production.
Filip Weymans, vice president of marketing said, “In the last year, Xeikon has launched several new innovations and products. Now, printers and converters are able to see our vision materialising, and what that can mean for them. The careful build and structure of our portfolio is about to bear fruit, and we are now ready to present more innovations that will open up a way toward a digital future, and ‘lights out’ production and manufacturing.”
Xeikon’s innovations include new product introductions in all different aspects of the print manufacturing workflow, including presses, services and workflow.
Trevor Crowley, general manager of Xeikon ANZ said, “This is about a coming together of all aspects of production to create an end-to-end digital manufacturing solution. Xeikon takes a holistic approach to print, and is showing how by joining the dots real efficiencies can be achieved.”
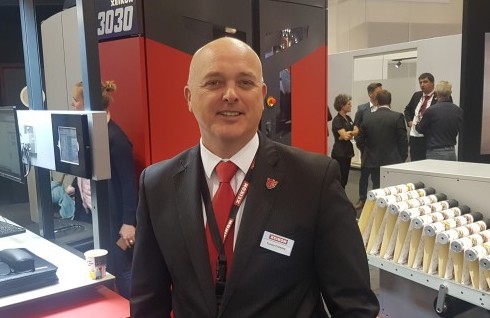
Xeikon Cheetah 2.0 dry toner technology: Now cloud-connected with man/machine and machine/machine interfaces, where the machines are in constant communication with each other, driving and monitoring print jobs with full automation. Earlier this year, Xeikon introduced two new models: the CX30 and the CX50 entry level dry-toner presses. With each cloud-connected solution, operators can monitor print manufacturing from anywhere on the shop floor by viewing the interfaces/dashboards 24/7 on a smartphone or any other device.
Panther 2.0 UV InkJet technology: New Panther models will include the Xeikon PX2200 and Xeikon PX3300, replacing the PX2000 and PX3000.
Xeikon Label Converting Unit (LCU) series: Within Xeikon’s portfolio, they are specifically designed for converting industries and printing businesses. The LCUs, formally named D-Coat, are also cloud-connected with machine/machine interfaces. There are various options to choose from; entry level, wide web, narrow web and high-end as well as more modular offerings. Again with each cloud -connected solution, operators can monitor print manufacturing from anywhere on the shop floor by viewing the interfaces/dashboards 24/7 on a smartphone or any other device.
Services
Xeikon is launching a selection of new services to add to its Solutions & Services (XSS) and aXelerate programs:
Xeikon (Performance Services) XPS will be offered first in North America. Xeikon Performance Services will be included as a standard for the first 6 months with all press investments. This is intended to help printers and converters identify which aspects of production need their attention. This software will highlight and visualise any key feature that need adjusting, including maintenance issues, training schedules or applications check. This service will be offered to support customers in their digital start-up phase. It will also provide Xeikon with the information needed to help their customers become operational faster when embarking on their digital journey.
Xeikon says its XCS Pro 2.0 is a cloud-connected breakthrough in colour management, it is an automated toolbox for the highest quality printed products. Extra capabilities include full automation for ‘on -the -fly’ profiling, colour profile monitoring and adjusting. It is now possible on a Xeikon press to automatically recalibrate the colour profile when an issue arises. The operator is alerted automatically, and the problem is automatically escalated to the production manager if it persists. XCS 2.0 can now be used for making colour profiles on a variety of different platforms such as a flexo press, offset press, screen printing with digital or any competitors press. This extends what can currently be achieved and expands the variety of applications and materials that can be worked with. The Xeikon XCS 2.0 also has the advantage of simplifying the process for the printer and manufacturer as it covers all their needs for high-end color management.
Workflow
A fundamental and key component of the workflow is Xeikon’s X-800 Digital Front End (DFE). The X-800 unifies every facet of Xeikon’s digital portfolio. Xeikon is now extending the capabilities of its X-800 to expand and enhance the range of possible applications. The label version of the X-800 will now include Xeikon Vari One variable data workflow, and combine it with Panther durable haptic printing and with Xeikon’s FEU (Fusion Embellishment Unit). Xeikon says this development is set to offer the highest levels of variable imagery available today. With this capability, the X-800 will drive both the Panther and the Cheetah series of presses towards digital transformation.
Weymans concludes, “With our latest innovations, printers and converters will be able to address the current and future needs of print buyers and brand owners. Having clear insight into their production environments means they can monitor progress and make quick and flexible decisions on the fly. This is why digitisation can be a game changer.
“When we install the first digital press at a company's site, we are with that company every step of their growth journey. They quickly realise the productivity, growth and profit benefits of implementing a fully automated digital print manufacturing process. Everyone knows that making changes in a company’s strategy and operations can be difficult. Xeikon stands as the go-to advisor for printers and converters looking to the future for their growth and sustainable profitability.”