COFFEE KEEPING CONTENT COMING
The latest round of press conferences at drupa have highlighted the innovation that is the order of the day on the stands, and in particular in the portfolios of major print players Mimaki, Fujifilm, Koenig & Bauer, Konica Minolta, and MGI.
A trip to Germany sounds exciting, and it is, but it takes some shoe leather to keep up with all that is going on, some auto filters in the brain to divert PR hyperbole from the real stories, and copious amounts of coffee in the press centre to keep going. Fortunately at a heavily subsidised half a euro each in journo central, copious cups of coffee are affordable.
Mimaki: We are the future
Mimaki, manufacturer of wide-format inkjet printers and cutting machines for the sign/ graphics, industrial, textile/ apparel and 3D markets, staged a press conference with a difference – no powerpoint slides made for a refreshing change. Instead, media visited the vibrant stand and chose the area they wanted to know more about.
Every company at drupa has a tagline, Mimaki's was the somewhat bold 'We are the future of print.'
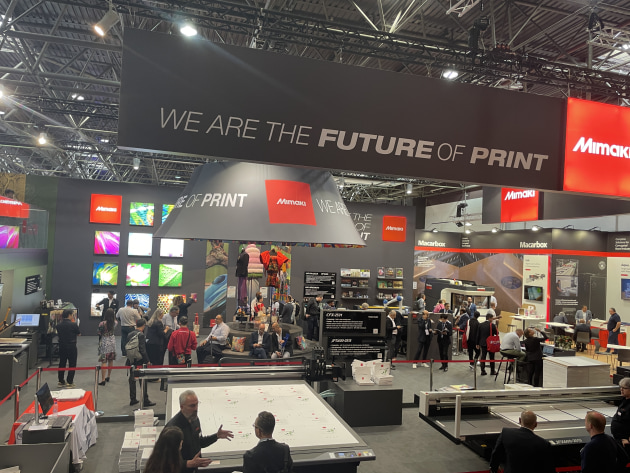
Print21 joined the sustainability session. Here we learned about Mimaki’s new textile pigment transfer printing system, Trapis, a waterless digital textile printing technology. It was explained thus: Trapis provides a simple two-step process, consisting of an inkjet printer and a calender. The design of choice is printed by the inkjet printer with a dedicated ink onto transfer paper, which is then transferred to the application via a calender.
Unlike both analogue and digital conventional dye-printing methods, Trapis generates almost no wastewater, only that which is produced during the printer’s automatic maintenance. Since no pre-treatment or washing of the fabric is required, this saves around 14.5 litres per square metre of water when compared to digital dye printing.
This also eliminates the need for wastewater treatment facilities, which can be both expensive and constrictive when it comes to where the solution is installed. Due to the smaller size, it is possible for the Trapis system to be installed in a limited space, or even at the front of a printshop.
But wait, there’s more… as the process only involves printing and transferring, it does not require specialised skills to operate when compared to the more complex seven- or eight-step system for digital and analogue conventional printing. The lack of a fabric conveyor belt in the system further minimises the need for time-intensive maintenance.
Trapis enables print on a wide range of materials, including natural fibres like cotton and silk in addition to blended fabrics, with just one type of ink, so the process can be flexible and adapt to customer demand, even with multi-material short runs
Fujifilm: Discovering a different way
On one of the biggest and busiest stands at drupa, imaging giant Fujifilm – which is marking 90 years in business at drupa – is impressing visitors with a host of new print solutions in commercial, wide format and packaging hardware, software and consumables.
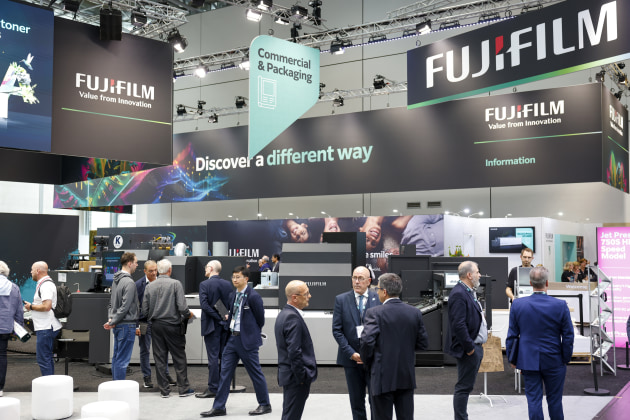
The company has launched the world’s first B2 sheetfed toner press, its first digital flexibles press, as well as new flexo plate, new inkjet heads and a new XMF workflow.
The new toner-powered B2 Revoria GC 12500 joins the B2 inkjet Jetpress that the company launched a decade ago, and which now has 300 systems running around the world.
Fujifilm has also launched upgrades to its Revoria 1120, which currently prints in six colours, adding new specialty colours to enable it to print CMYK plus RGB. The company says it also comes with the world’s first pressure sensitive adhesive, which it says will work in applications such as direct mail.
Also on show is a new Jetpress 1160 continuous feed printer, available outside of Japan for the first time. In the demo at drupa, it is printing on both coated and uncoated papers, and comes with a paper stabiliser to overcome paper feed difficulties.
The new digital inkjet packaging press for flexibles is the Fujifilm FP790, which runs at 50 metres a minute at 1200 x 1200dpi on flexible film. Released in Europe earlier this year, five systems have so far been installed.
In wide format print Fujifilm is showing the Prime flatbed, Prime hybrid and Ultra roll-to-roll systems on its stand, along with a new Aquaforce ink, which is an aqueous ink with UV curing.
Packaging is where it’s at, says Koenig & Bauer
Addressing members of the press at drupa, “we are everywhere” was the opening gambit of Koenig & Bauer CEO Dr Andreas Plesske, referencing the world’s oldest press manufacturer’s capability across all printing technologies and across all substrates.

Koenig & Bauer may be the world's oldest press manufacturer, but its stand was the most modern, marking a radical departure from its previous drupas.
Dr Plesske said that packaging is the main growth market for print, citing Smithers figures that put the current CAGR for packaging at 3-4 per cent, and he made it clear that it is to packaging that the company will be directing its R&D and investment.
As a result, the focus of the Koenig & Bauer’s 4000 m² drupa stand is on packaging and digital solutions, including its demonstration of an end-to-end packaging workflow with offset, digital and flexo printing and finishing. The company is launching ten new digital products and technologies.
In line with the packaging digitalisation trend, Koenig & Bauer is showcasing how connected packaging builds a bridge between analogue packaging and the digital world. Print21 visited the stand and spoke to market engagement manager Florian Stark, who demonstrated the company’s development of a platform based on Google cloud technology where brand owners can store digital information to individualise, personalise and enrich their printed packaging, alongside detailed product and manufacturing specifications.
Stark demonstrated how the smartphone activated app for end consumers acts as a bridge between analogue packaging and the digital world, and by making comprehensive product information available to the consumer by way of augmented reality, enhances the shopping experience.
Still in the digital solutions realm, this time across production automation, K&B is showing a virtual product configuration based on innovative automation technologies and a digital twin of its own production facilities, developed in partnership with Siemens. The objective is to accelerate development and commissioning processes and to raise customer support and after-sales service to a new level, the company says.
The new technology allows the collection and evaluation of detailed machine data and information on the condition of machine components. Using the feeder for a Rapida 106 medium-format sheetfed offset press as an example, Koenig & Bauer is giving drupa visitors a first glimpse of the future with its standardised and modular automation platform, and demonstrates real-life predictive maintenance cases and performance dashboards for individual machine components.
The platform is currently still in the development phase, but shows how Koenig & Bauer intends to respond to global megatrends and lead the group into a new era.
Konica Minolta and MGI: Printroom of the future
Claiming to have brought to drupa “the most advanced end-to-end smart factory digital production lines ever shown in public”, Konica Minolta and MGI Digital Printing Systems (MGI) have over 30 live running machines on their joint 2300 square-metre booth, the seventh largest at drupa. The goal is to demonstrate how separate processes such as foiling, varnishing, printing, folding, and drying can be combined into one full integrated production run; this has been amply achieved through the complete single-pass factory set up that takes the form of MGI’s AlphaJet, a centrepiece on the stand, and gives a glimpse of Konica Minolta and MGI’s vision of the print room of the future.
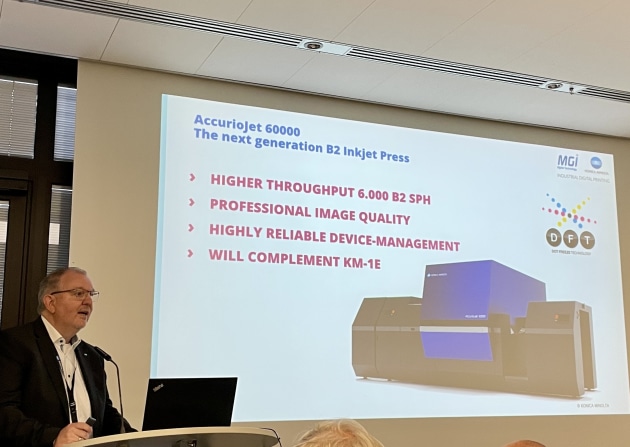
Digital printing is front and centre, as Olaf Lorenz, GM International Marketing, Konica Minolta Business Solutions Europe, told the media: “[Our] mission is to promote the shift from analogue printing to the use of digital printing, thereby creating a world in which high-value-added printed materials are printed efficiently and the environmental impact is minimised.”
Making its debut at drupa is Konica Minolta’s AccurioJet 60000, a HS-UV inkjet press with a capacity of 6000 sheets per hour and offering both-side printing capabilities, ensuring versatility and efficiency in printing operations, while delivering “excellent image quality”. The use of Konica Minolta inline sensors and a spectrophotometer allows continuous monitoring and control of the printing process to ensure consistently high quality.
Also new at drupa is Konica Minolta’s AccurioPress C84hc press, which uses high chroma toner that prints bright vivid colours consistently. According to KonicaMinolta, it is the “world’s only” platform using the new toner free of the restrictions imposed by the colour gamut of ordinary toners. Target customers include commercial printers, dedicated design houses, advertising agencies, corporates, and brands.
Other star performers on show include the multi-award-winning toner systems such as Konica Minolta’s AccurioPress C14000e toner press for high-volume production with more than 2200 global sales already and the AccurioLabel 400 – part of a single-pass portfolio that has already secured more than 1500 sales worldwide
Konica Minolta says these and other systems have helped underpin its reputation as a major player in digital printing as it continues to make further inroads into commercial and industrial printing markets using inkjet and toner technologies.
Mimaki: We are the future
Mimaki, manufacturer of wide-format inkjet printers and cutting machines for the sign/ graphics, industrial, textile/ apparel and 3D markets, staged a press conference with a difference – no powerpoint slides made for a refreshing change. Instead, media visited the vibrant stand and chose the area they wanted to know more about.
Every company at drupa has a tagline, Mimaki's was the somewhat bold 'We are the future of print.'
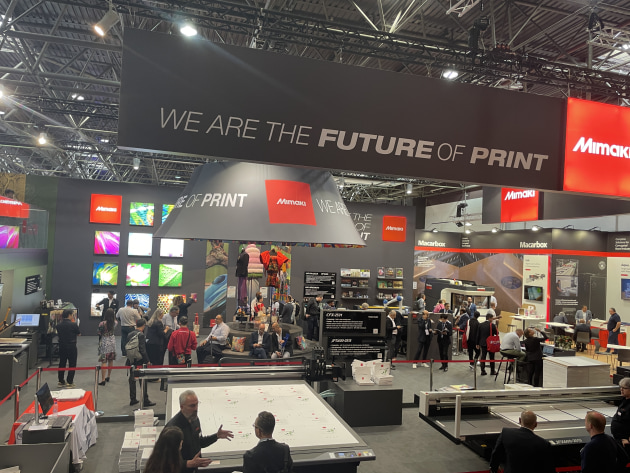
Print21 joined the sustainability session. Here we learned about Mimaki’s new textile pigment transfer printing system, Trapis, a waterless digital textile printing technology. It was explained thus: Trapis provides a simple two-step process, consisting of an inkjet printer and a calender. The design of choice is printed by the inkjet printer with a dedicated ink onto transfer paper, which is then transferred to the application via a calender.
Unlike both analogue and digital conventional dye-printing methods, Trapis generates almost no wastewater, only that which is produced during the printer’s automatic maintenance. Since no pre-treatment or washing of the fabric is required, this saves around 14.5 litres per square metre of water when compared to digital dye printing.
This also eliminates the need for wastewater treatment facilities, which can be both expensive and constrictive when it comes to where the solution is installed. Due to the smaller size, it is possible for the Trapis system to be installed in a limited space, or even at the front of a printshop.
But wait, there’s more… as the process only involves printing and transferring, it does not require specialised skills to operate when compared to the more complex seven- or eight-step system for digital and analogue conventional printing. The lack of a fabric conveyor belt in the system further minimises the need for time-intensive maintenance.
Trapis enables print on a wide range of materials, including natural fibres like cotton and silk in addition to blended fabrics, with just one type of ink, so the process can be flexible and adapt to customer demand, even with multi-material short runs