SCHUR INSTALLS NEW 10-COLOUR FLEXO PRESS
Schur Star Systems Australia has installed and commissioned a new Windmoeller & Holscher Miraflex 10-colour flexographic press, the first of its kind in Australia.
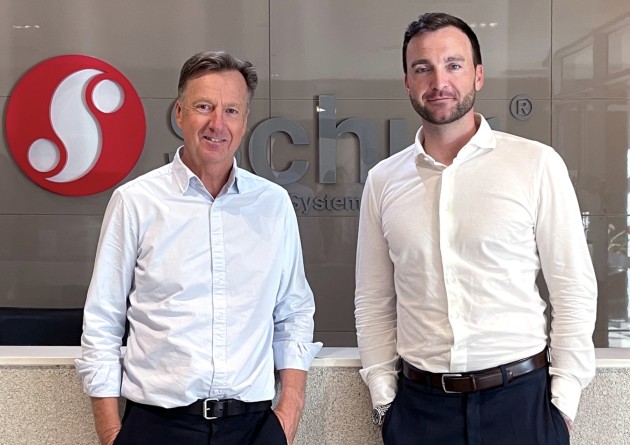
The new press is part of a $25m investment at the company’s Melbourne production facility, aimed to meet growing demand for the company’s flexible packaging solutions.
On the traditional flexibles supply side, the Schur portfolio – which comprises the bulk of its Australian business – includes printed laminates, lidding films, and pouches. It is this part of the business that the company says will see growth because of the new 10-colour flexo press, which has a gravure inline unit.
The new W&H Miraflex press incorporates electric driven hot water drying, rather than traditional gas, which combined with the solar panel installation, ensures the most efficient use of energy, says Schur.
The new flexo press joins a long-serving Uteco flexo press on the floor, but with double the capacity of the old press, it significantly ramps up Schur’s printing and converting capability.
Paul Quinn, CEO of the Australian business said, “The press is as highly specified as it could possibly be, giving us capabilities that are unusual in the market.
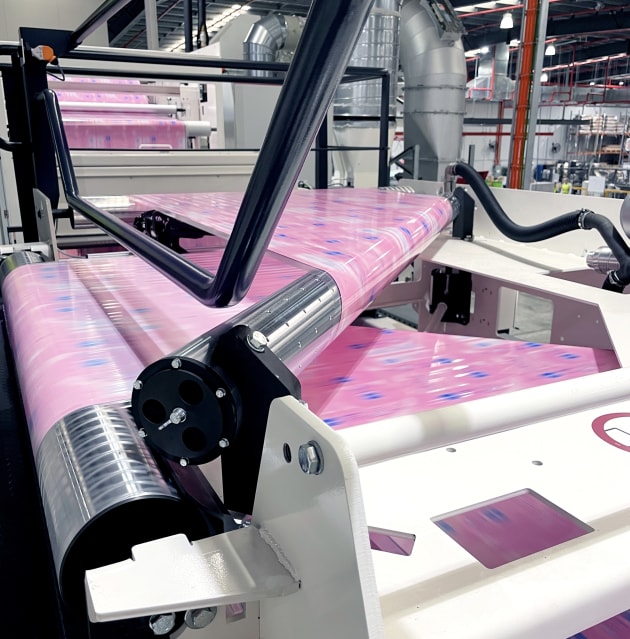
“For instance, it allows us to apply cold seal on printed materials in one pass – we print, turn the film and apply the cold seal on the other side, all in one pass. The same applies to varnishes, and heat seal coatings – we see a lot of growth in the future for these heat seal coatings being applied to papers, for example, whereas traditionally those types of materials had to be put through presses twice, or once through the press and once through a laminator.”
Quinn adds, “We believe there will be a lot of growth in cold seal, because it allows you to run at high speed when using recyclable materials, which can be a challenge on other presses.”
Schur’s Australian operations were established when the Danish Schur group purchased Burgess Printing & Packaging in 2016, as it sought to expand the footprint of its proprietary Schur Star concept into the ANZ region. It acquired an existing flexible print and packaging operation with a customer base across the food, beverage, pharmaceutical, chemical and industrial sectors, in a move it said made “strategic sense.”
Johan Schur, co-director of the company, flew in from Denmark to join Paul Quinn, CEO of the Australian operation, for a series of meetings with customers who they say have been singularly impressed by the capabilities of the new line.
Schur describes the company as a ‘dual-role’ business. “We are a flexible packaging company supplying printed flexible materials, but we also sell our Schur Star system, which includes pre-made flexible bags custom-made for filling on a linked production line, providing producers, packers and growers with the ability to change bag size and functionalities.”
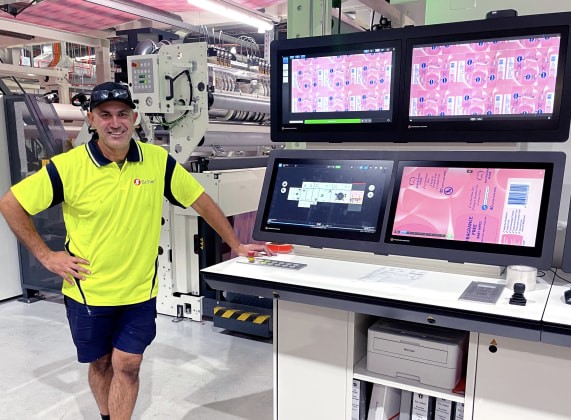
Johan Schur says Schur International has a philosophy that all its factories should be world class facilities and Australia is no exception. The investment in the new press and the facility upgrade totals $25 million, with the modernisation including new air conditioning, heating and ventilation systems throughout the plant, as well as rooftop solar panels.
He goes on to note that in long run jobs, such as for high volume sectors like confectionery – where there has been a move by some major players to trial paper-based flexibles – cold seal is a viable solution for printing at high speed.
Johan Schur adds, “Since our entry into the Australian market, the business has continued to enjoy year-on-year growth, and the investment we have now made taps into the potential we see in this market, especially as Australia follows the trends we see in Europe in sustainability and automation."
“I think it’s important to note that we did not just buy a Miraflex printing press, we bought one-and-a-half presses, because the extra gravure unit adds 30 per cent to the length of the press footprint. This is a big deal to us. In the flexibles market we compete against imported goods and if we can’t provide competitive pricing to our customers, we cannot sell more sustainable solutions.
“The ability to run the substrate through the press once at high speed, rather than twice at a lower speed, is a huge factor as we move to grow our business and our sustainability profile with customers.”
Quinn adds, “There’s a job we’re running today on the new press at four times the efficiency than we did on the old press, because we had to run it through the old press twice at half the speed. So that has a major impact on labour costs as a percentage of our sell price. And obviously this reduces running time and energy.
“The new press is also way more advanced in terms of the speed to set up a new job. So, the old press might use 1000 meters of film, but by the time you’ve colour-matched and got the impressions set and all that type of thing, the new machine will use more like 100 or 150 metres of film, a major saving in time, materials, and the amount of ink used per job setup. So, there’s efficiencies at every level.”
Quinn believes the new press will serve to strengthen the company’s market position, because it will deliver efficiency and scale, allowing Schur to be more competitive.
“It’s not just about price, it’s about customers coming on the sustainability journey with us and enjoying the benefits of the technology in this press, allowing us to optimise productivity, reduce energy usage and waste, while eliminating print imperfections.”
Also counting in the company’s favour is the fact that Schur recently achieved ISCC accreditation, allowing it to use and process PCR-content. This is a bit ahead of time in the Australian market, with PCR films in short supply, but the company will be ready when materials do become available and will enable its customers to prepare for upcoming regulations that will mandate recycled content. The Australian business, of course, can take guidance from the global group, which, headquartered in Europe, is across the more advanced recycling regulations and mandates in that market.
Another point of differentiation for Schur in the Australian market is that it manufactures its own printing plates, boosting speed to market with efficient lead times. “Our turnaround and responsiveness to customers is first class, putting us well ahead of our competitors from offshore markets like China,” Quinn adds.