Grand Print gears up with Océ Arizona and ProCut
NSW sign and display company Grand Print Services is making a major investment with a top-of-the-range Océ Arizona 1380XT flatbed printer, and a ProCut 3200L digital cutting system.
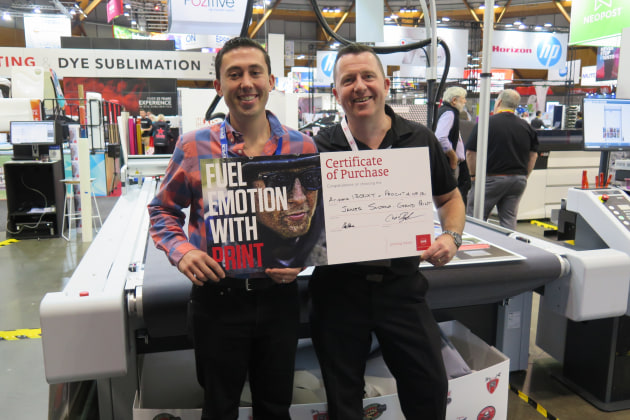
The company is based on the NSW south coast with a new factory in Gerringong. It was only established four years ago, when owner James Sultana moved his young family there for a more relaxed lifestyle than they enjoyed in Sydney.
The new equipment and new factory is a significant leap for Grand Print, which started with a chance encounter soon after the family’s move. “I was looking for work and a connection here offered me some signage installation management work,” Sultana explains. “With my background in the sign and display industry, project managing installations and expos, it seemed like good work to pick up while I looked for something more permanent.”
Pretty soon, that stop gap became almost a full-time occupation, and his clients started to ask for a full turnkey solution. “I had no plans to get back into production, and starting a business was the furthest thing from my mind, but eventually I found a niche in the market to provide a high level of service for the entire production process, as opposed to just supplying print or just managing the install,” he explains.
For a while, outsourcing the print sufficed, but by late last year, it became apparent that the convenience and control of his own manufacturing facilities would make life easier.
An initial investment in a roll-to-roll machine helped somewhat, but there was still an enormous amount of work that had to be sent out – or, alternatively, assembled manually in-house, like corflute signage, which involved a time-consuming process of printing decals, then mounting on the rollover table and manually trimming
After doing some research – prioritising flexibility and reliability – he found the solution in the printer and cutter duo from Océ Australia.
“We had talked to our Océ BDM, Chris Bowden, about the solutions, and we ended up taking a trip to Melbourne to the company’s new Customer Experience Centre, where we were able to see both machines in action,” Sultana explains.
“Chris worked with us to really understand our business requirements and recommend a solution which would answer those needs – and the new workflow from Océ makes the whole solution seamless.”
As a key innovation centre for Canon, a global leader in consumer and professional imaging, Océ invests heavily in R&D. The new Arizona 1300 range draws on more than a decade of flatbed development, to provide the sign and display market with a printer that the company says is more versatile than competitors, and more productive.
As well as handling a wide range of media, the high-quality printer’s application versatility is enhanced with innovations like Touchstone software which enables 2.5D print for raised and textured surfaces, and LED curing which speeds make ready and enables the use of Greenguard-certified LED-UV ink, while according to Océ, the Arizona Xpert job preparation software turbo-charges productivity.
“The flatbed capacity will be a game-changer for us, expanding the range of work we can handle and increasing options for our clients, and I’m really excited about the range of products and print finishes it will allow us to produce,” said Sultana.
The ProCut 3200L – from the Océ range of digital cutters, can cut, mill, polish and engrave on media up to 60mm in depth. The ProCut pairs with the Arizona for seamless large format workflow from prepress to finishing, providing automation and ease of use, making it the finishing companion for this flexible printer.
“The ProCut will be an amazing addition, increasing our accuracy and capacity to trim and finish both rigid and flexible products in-house and improving our productivity and profitability,” he adds. “And it’s so easy – we can just print directly onto whatever substrate we’re using, scan the barcode into the digital cutter, and we’re done.”
As well as giving James control over production by bringing a high percentage of jobs in-house, the dual investment also provides capacity for future growth and, together with the planned addition of some new staff resources, sets the stage to give him some much-needed time to reflect on his future business strategy and planning.
“I was talking to someone the other day about how busy I was at work, and they asked me if I really wanted to be spending long hours at the factory every day for the rest of my life. And of course, I don’t – having more time with my family was the reason we moved here in the first place,” he says.
“This new technology from Océ, backed by their technical expertise and local service support, will put me back in control of my future – and that’s a great feeling.”