FIBRE SET FOR PACKAGING GROWTH
Fibre-based packaging is set for sustained growth as a key packaging material, with corrugated, folding carton, liquid paperboard, flexible paper and moulded fibre all forecast for an upswing, according to analysts Smithers.
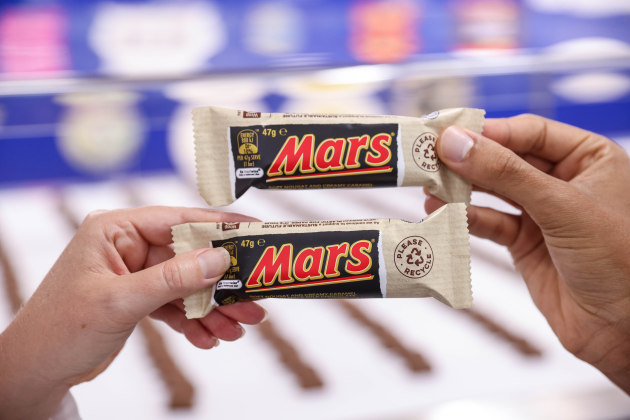
The current and future market outlook for such pack formats is examined, in detail, in a new study – The Future of Fibre-based Packaging to 2027 – from Smithers, the leading consultancy for the paper, plastics and packaging industry.
Its exclusive data set shows that in 2022 world consumption of corrugated, folding carton, liquid paperboard, flexible paper and moulded fibre packaging totalled 264 million tonnes in 2022. Total value in that year was US$425bn (A$621bn).
Organic growth coupled with some format shifting will push combined world value up to $503bn in 2027, equivalent to a 3.4 per cent compound annual growth rate (CAGR). Volume consumption will increase slightly faster at 3.6 per cent CAGR to reach 316 million tonnes in 2027.
Australasia holds a modest share of this market, equivalent to 2.26 million tonnes in 2022, worth US$3.2bn. Demand for these in the region will increase at a +2.6 per cent cent CAGR (by value) faster than in any other developed market.
Fibre formats
Tom Hallam, project director, Packaging Consultancy at Smithers, said: “Worldwide, sustainability is now a watchword across the packaging industry, it is increasingly a must-have for brands, rather than an ancillary benefit that only interests a minority of ethically switched-on consumers. Many brands have set tough ESG goals that they will need to meet by 2025 or 2030. How realistic or achievable these are is open to debate – but there is a clear priority to meet consumer expectations for greater recyclability. This is driving new interest in swapping from plastics to paperboards, coupled with more R&D spending on coatings, application technologies, and moulded fibre.”
By both volume and value, the most significant fibre pack type is corrugated cardboard. Its CAGRs for 2022 to 2027 are projected at 3.5 per cent by volume and 2.7 per cent by value. Its overall proportion will decrease over the period due to faster growth rates for other product types, coupled with continued lightweighting of the board, which reduces volume consumption.
Higher growth rates will be seen in folding carton (CAGRs of 4.6 per cent and 4.7 per cent by volume and value, respectively) and moulded fibre (CAGR of 5 per cent by both volume and value); the growth of these products is driven by changing lifestyles and their effectiveness in replacing single-use plastics.
Corrugated Growth
The global pandemic has seen corrugated packaging take a higher profile. Globally the market was largely able to absorb the losses seen in transit shipment volumes with new sales in to direct-to-consumer e-commerce shipment. Sales of corrugated into e-commerce reached US$51bn; 80 per cent of the global total in that sales channel.
There is new interest in developing more consumer-facing corrugated retail packs. The most immediate application has been found in formats for retaining multipacks of FMCGs, especially heavier items such as beer, bottled water, or tinned goods. These provide a more sustainable option to existing solutions, like wrap films or six-pack rings. This is technically undemanding, corrugated is certainly strong enough. There is competition, however, from folding cartonboard or recycled plastic retaining fixtures; while in beer sales some brewers are using adhesives to simply stick multi-sale packs together.
Hallam added, “Primary packaging is more of a challenge when substituting for plastics. Some work is progressing on coatings to improve moisture and water resistance to corrugated sheets, but the same technology is also often suitable for cartonboard, paper or moulded fibre materials.”
There is a continuing trend for corrugated board towards lightweighting – reducing the physical mass without negatively affecting the strength of the packaging. The composite structure of corrugated cardboard makes this relatively easy in technical terms. It can be done by choosing different combinations of liners. This is allowing microflutes to challenge thicker folding carton grades in some applications.
Folding cartons
Folding cartons – paper grades 0.3mm or thicker – are a mainstay of consumer packaging due to their ease of use, good print surface and convenient disposal. They represent the second largest segment of the fibre-based packaging products, both by volume and value.
Their versatility is boosted by the range of functional coatings already commercially available. These can give a much better print surface for brand graphics, finishes and embellishments; making them a preferred option in standard and premium FMCG segments.
Currently around 80 per cent of cartonboard is used in folding carton applications. Across the next five years, the most promising applications will be found in primary food packaging as an alternative to single-use plastics. These are not a universal solution, and brands contemplating a switch need to carefully gauge the need for additional features like functional coatings or internal liner bags.
In 2023, some of the fastest developments will come in confectionery, with brands opting for folding cartons, as well as flexible papers, in place of polymer pouches.
Liquid paperboard
Aseptic cartons formed from liquid paperboards are made from laminating paperboards with polyethylene (PE) film or aluminium foil on one or both sides. This presents a high barrier to the liquid and allows a majority paperboard pack to be used for a variety of wet foods, milk, milk substitutes, fruit juices, yoghurts, and other liquid foods.
While both the paperboard core and aluminium are widely recycled, liquid paperboard is the fibre format that presents the most problems in terms of recovery at end-of-life. The challenges of separating the two materials cost-effectively means these are rarely recycled. Liquid paperboard suppliers have set up their own trial recovery schemes for existing formats, but availability is very limited, in one of the smaller segments of the paper packaging market.
In response, several manufacturers – Elopak, SIG Combibloc and Tetra Pak – are trialling new constructions without an aluminium layer for all products. These instead rely purely on PE barrier layers, that are easier to separate in mixed recycling schemes. Other R&D priorities include developing coatings from micro-fibrillated cellulose (MFC) or new biopolymers, such as polyethylene furanoate (PEF).
Flexible papers
With flexible plastics increasingly recognised as the least recyclable material sets, there is potential for the latest generation of specialty papers. Several of these are being marketed as direct replacements for plastics, but there are multiple technical challenges, around barrier performance, processability, heat sealing, and printing.
These are being tackled progressively, but the actual market displacement of flexible plastics will be limited over the Smithers forecast period. High-barrier paper lines are available, including retortable pouch designs, but adoption in developed markets will be largely eclipsed by growing use in developing regions. In nascent markets, where retail and waste collection structures are more basic, these still present the best option, especially when cold chain distribution and home refrigeration is limited.
Moulded fibre
Some of the most exciting developments in fibre packaging is coming from moulded pulp or fibre, with Europe a hotbed for innovation. This material has traditionally been limited in use to egg cartons and protective shipping components. These are sustainable as they can be made with up to 100 per cent recycled content, are cheap, fully recyclable, and even if they are not collected, biodegrade naturally.
The main commercial advantage is that as a moulded technology these can start to replace formed plastics in tray, tub, and even potentially, bottle formats. For primary packs, barrier performance and resistance to oven or microwave cooking are priorities for technical R&D. The other main challenge is to develop moulded-fibre forming lines that can match the speed of existing thermoformed plastics.